Why MEP Planning Early in Construction Saves You Big Costs Later
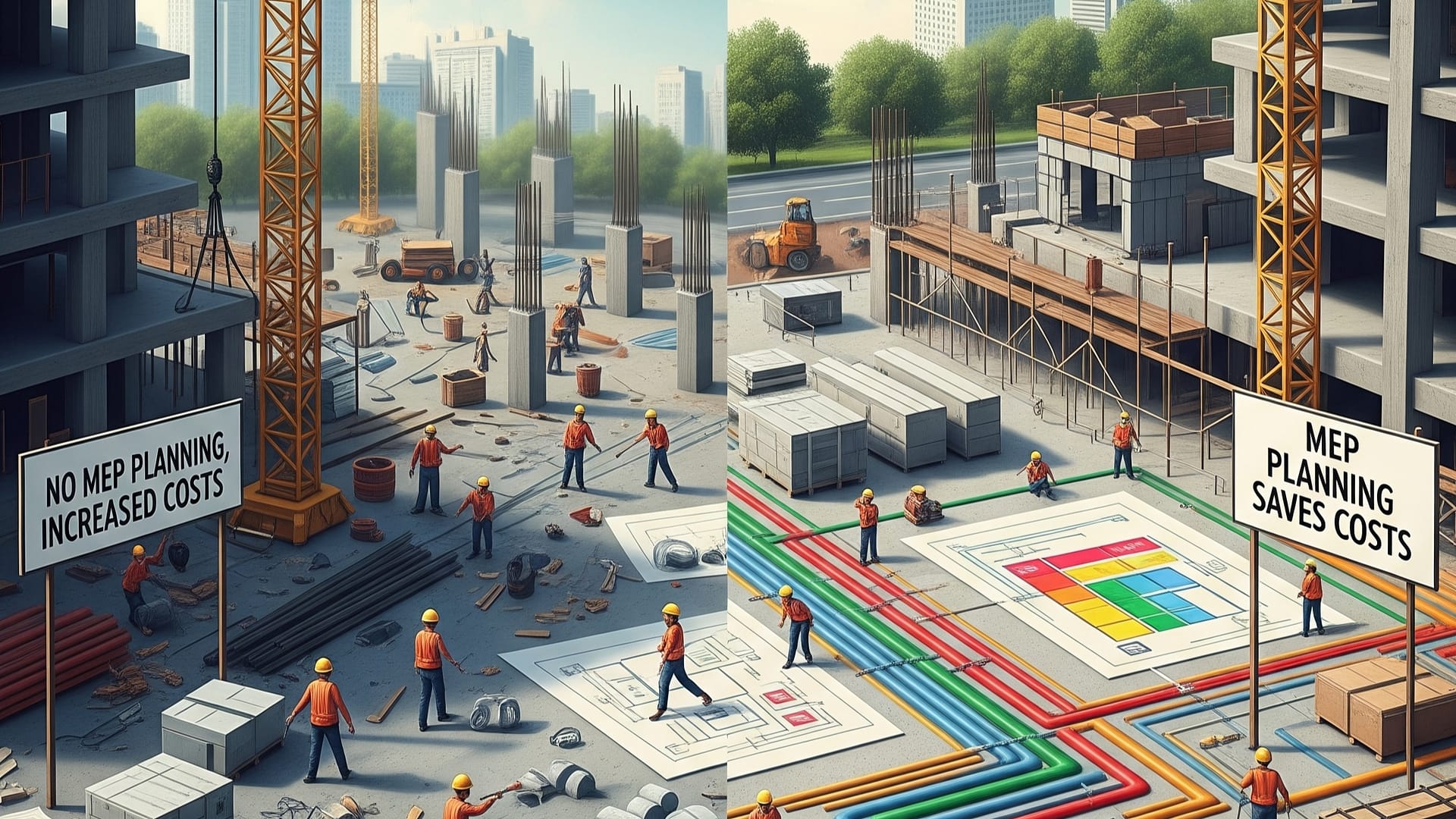
When starting a new construction project, most of the focus naturally goes into the architectural design, structural framework, and aesthetics. But one critical component that is often delayed — and which can later cost you a fortune — is MEP planning.
MEP stands for Mechanical, Electrical, and Plumbing. These systems are the backbone of any functional building. If you skip early MEP planning, you’re not just risking inefficiency — you’re setting your entire project up for cost overruns, time delays, and regulatory headaches.
In this article, we’ll explain why integrating MEP planning at the early stages of your project is not just smart — it’s essential.
What Happens When You Ignore Early MEP Planning?
Many developers or clients tend to treat MEP design as a “secondary” task, only to discover later that:
Ducts don’t fit the ceiling space
Electrical loads weren’t properly calculated
Plumbing interferes with structural beams
HVAC systems are underpowered or oversized
Local codes and compliance issues arise unexpectedly
Fixing these issues after construction has begun leads to rework, material waste, and project delays — all of which eat into your budget.
5 Reasons to Do MEP Planning Early
1. Avoid Costly Rework
Early MEP integration allows your team to foresee and avoid potential clashes between systems (like plumbing intersecting with electrical conduits). This reduces last-minute changes, contractor delays, and change order costs.
2. Improve Energy Efficiency
Energy consumption is a major cost over a building’s lifetime. When HVAC systems, lighting, and ventilation are properly designed from day one, you can optimize for energy savings and sustainability — which can also qualify your building for green certifications.
3. Ensure Better Coordination with Architects
When MEP engineers work closely with architects from the beginning, you get a harmonized design. There’s better utilization of ceiling heights, wall cavities, shaft spaces, and more — leading to a cleaner, more maintainable result.
4. Comply with Local Codes Early
Every region has specific rules about electrical load distribution, plumbing layouts, fire safety, and mechanical systems. Early MEP planning ensures your project meets all legal and safety codes without last-minute surprises.
5. Reduce Project Delays
Construction delays due to design conflicts or missing MEP documentation can stretch project timelines. Early planning ensures that all teams — structural, architectural, and services — are working from the same blueprint, minimizing downtime.
Real-World Scenario: The Cost of Being Late
We once had a client who brought us in during the final stage of structural design. Unfortunately, the ducts for the HVAC system couldn’t fit within the false ceiling due to low slab height. The solution? Break and rebuild — costing ₹4.5 lakhs in additional expenses and nearly 3 weeks of delay.
All of this could’ve been avoided with proper early-stage MEP coordination.
How We Help at A-Square
At A-Square, we specialize in MEP consulting and BIM coordination tailored to your project’s needs — whether it’s residential, commercial, or industrial. Our team works closely with architects, project managers, and civil engineers to ensure that your MEP systems are well-planned, efficient, and compliant.
📞 Need help with your current project?
👉 Click here to schedule or use the popup form on this page.
Final Thoughts
Don’t treat MEP like an afterthought. It’s not just about pipes, wires, or ducts — it’s about making your building functional, cost-efficient, and future-proof.
Plan your MEP early. Avoid regrets later.